The doctoral thesis of the student Aws Hashem Nimah from the University of Basra, College of Engineering, Department of Electrical Engineering, was discussed under the title: Design and Implementation of Multilevel PV Powered Inverter for Induction Heating Systems It included Induction heating IH is a technology for heating conduction metals without contact, which has been used in multiple applications in many fields. It has been used in industrial fields such as melting and welding metals, and manufacturing household appliances such as heating cookers, and water heating systems. It has also been used in the pharmaceutical and food industries by including the IH technology in canning system. The medical field has used IH technology for treating cancerous diseases.
In this thesis, the design and implementation of IH system using a multilevel inverter as a power supply is covered and discussed. The IH system consists of four major parts: DC voltage source, multilevel power supply inverter, a phase lock loop controller to track and lock resonant frequency, and finally the induction coil.
This work includes many parts, in the first part, the IH coil is designed and simulated using the Ansoft Maxwell with ANSYS workbench programs. This simulation program is used to study and analyze the behavior of the working coil and workpiece during the heating process. Eddy current and magnetostatic solver is used to measure the Ohmic loss, current density distribution, and magnetic flux distribution. The second part is modeling and simulating the proposed reduced switches five-level inverter using MATLAB. The proposed topology is tested and compared with other two conventional topologies (cascade H bridge and neutral point clamped inverters). The third part, is the modeling and simulation of a phase lock loop controller to track and lock on the resonant frequency using MATLAB SIMULINK. The two signals used for the PLL controller are the inverter output voltage and capacitor voltage. A comparison is made for two induction heating systems, one used 5-level inverter, and the other used full bridge inverter.
The last part is design and implement the prototype of induction heating system that can operate at a range of frequencies (29.92 to 90 kHz) and power 1kW. The FPGA NI-myRIO controller with LabVIEW interface program is used to implement the suggested PLL controller and compare it with five different types of controlling methods (Proportional Integral Derivative, Slide Mode Control 1, Slide Mode Control 2, Super Twist Control, and Integral Slide Mode Control). The experiment results show that the software PLL controller consume low power as a compare with other control technique. It successfully heated the different workpieces made from (Copper and Iron) in a very short time.
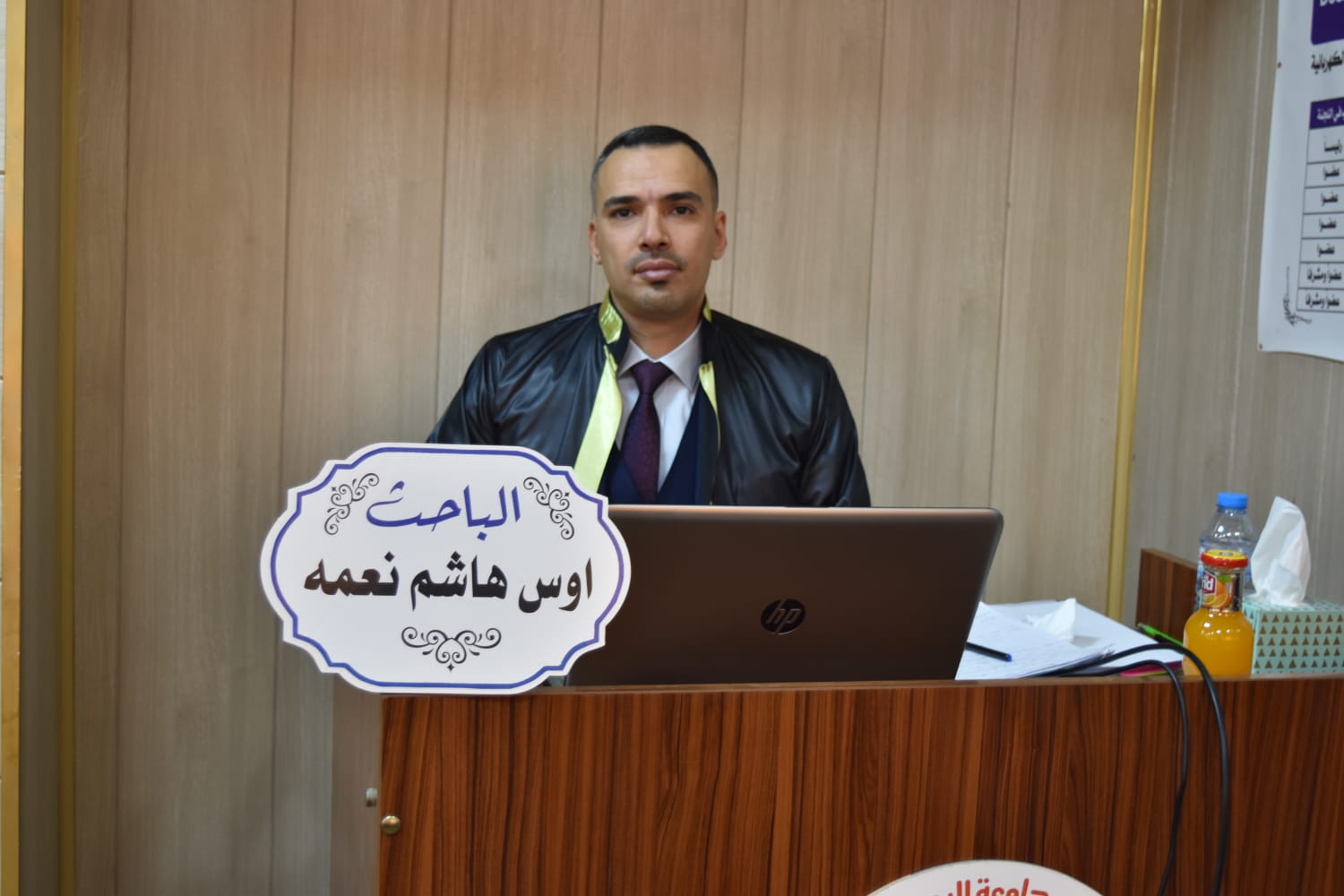