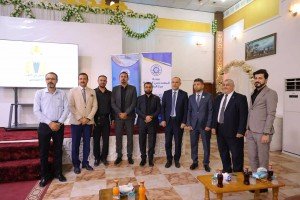
Dr. Ahmed Abdul Karim Al-Sahlani, a lecturer at the College of Engineering, University of Basra, in cooperation with lecturers Tawfiq Yap Yun Hen from the Research Center for Catalytic Sciences and Technologies (PutraCat), College of Science, University of Putra Malaysia (UPM), 43400 Serdang, Malaysia and Muhammad Ghassan Abdul Karim Al-Sultan from the University of Basra for Oil and Gas
College of Industrial Management for Oil and Gas Chairman of the Department of Oil Project Management Abdul Karim Ghassan Abdul Karim Al-Sultan Research Center for Catalytic Sciences and Technologies (PutraCat), College of Science, University of Putra Malaysia (UPM), 43400 Serdang, Malaysia and Omar Ghassan Abdul Karim Al-Sultan and Tony Agustiono Kurniawan published a scientific research in a reputable international journal entitled Exploring Innovations in Wind Turbine Design for Sustainable Energy, which includes Renewable energy (RE) sources are in high demand due to their eco-friendliness and sustainability. Wind is an alternative energy source that can be captured using a wind turbine (WT). Wind turbines (WTs) are classified into two types: Horizontal axis (HAWT) and Vertical axis (VAWT). Large-scale WTs typically use a Continuously Variable Transmission (CVT) system as their gearbox system, which is highly efficient. However, it is difficult and expensive. Meanwhile, most small-scale WTs available in the market use a single-speed gearing system, which indicates no gear ratios are altered, thereby decreasing the energy efficiency and causing gear failure. They realise that critical WT components, such as the gearbox parts, require constant monitoring. These components require significant repair and maintenance. A fixed-speed WT generator is directly associated with the electrical grid, and it has various limitations, including its inability to control reactive power or grid voltage. This study proposes an AGS for VAWTs to enhance energy capture. The design of the VAWT gear-and-clutch system was conceived, manufactured, and analysed in this study. The gear-and-clutch system was established with the gear-and-clutch formula. The system was then built in SolidWorks and manufactured using a 3D printer for VAWT. A crucial component in the design of HAWTs is the gearbox system, which serves the essential function of stepping up the low rotational speed of the turbine blades to a higher speed suitable for electricity generation by the generator. The researchers altered the gear ratios, and the number of gears was increased to 2. The gear consists of centrifugal clutch that helps to change the automatic gears. The wind speed (WS) received was initially increased until the VAWT began to spin (20 m/s), then decreased to 0 m/s. The ability of the VAWT to efficiently harvest energy was determined by contrasting the amount of power and voltage that it outputted when it was and was not fitted with an AGS. The results suggest that VAWTs equipped with an AGS and centrifugal clutch are more reliable and efficient. More specifically, the AGS reduced the WS required to make the VAWT spin by 7 m/s (to 13 m/s) and it was able to continue spinning even after the WS decreased. The power and voltage outputs further demonstrated that it could harvest energy with maximal efficiency while losing minimal energy.