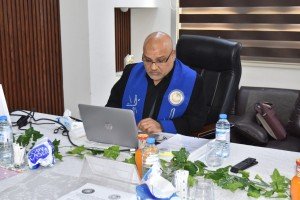
A master's thesis was discussed in the College of Engineering at the University of Basrah (simulating residual stresses for stainless steel tubes 316). Analyzing the residual stresses generated during the welding process and selecting the best welding standards that give the lowest Residual stresses in SS316 pipes with diameters of 50, 75, 100 mm and thicknesses of 4, 5, 7 mm at respectively, which were manually welded using welding wire (316) and using metal arc welding The protected (SMAW) in a single-lane butt link with different values of currents. The shielded metal arc welding process involves heating, melting and solidifying the base metal and filler material in a fusion zone localized by means of a transient heat source fragmentation of the junction between the main links. Finite element methods are used in ANSYS software for residual stress distribution in welding. The use of Iranian mechanical and thermal theory. A permit is prohibited from outside The thesis concludes that the residual stress distribution in the weld center is continuous and upward, with a value of about 1738 MPa for the first return. In addition, the The residual pressure at the boundary between the heat affected zone and the weld rises to a maximum value It is about (3799.6 MPa). On the other hand, the magnitude of residual stress decreases in the region significantly affected by temperature and achieves a minimum value at a position (20 mm) with a value close to zero.